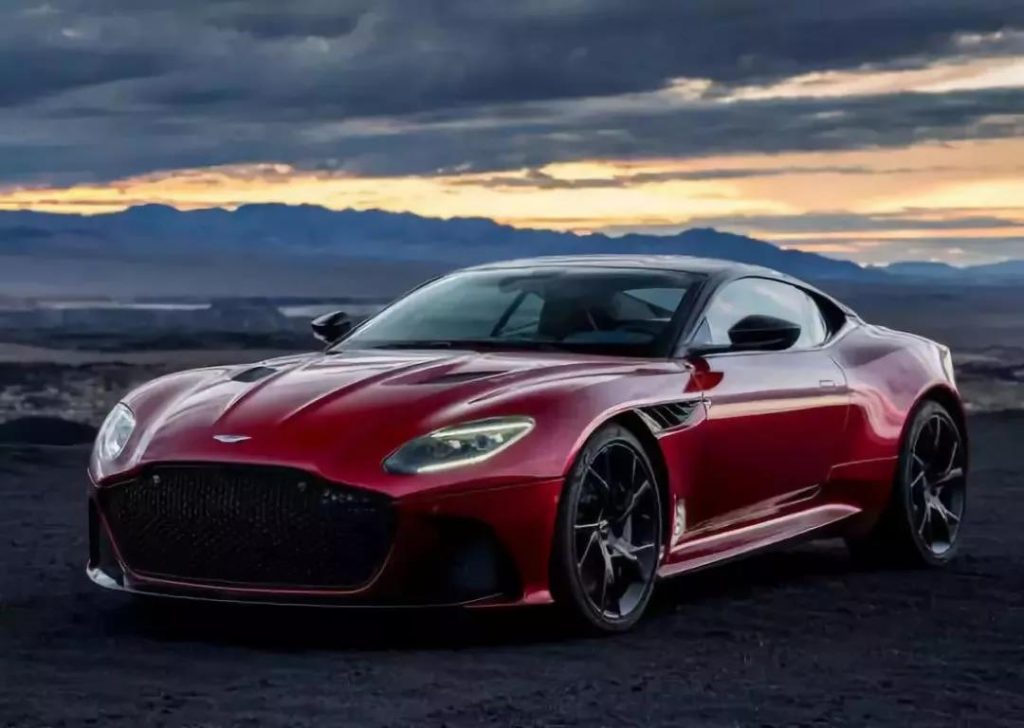
汽车车身约占汽车总质量的30%,空载情况下,约70%的油耗用在车身质量上。因此,车身变轻对于整车的燃油经济性、车辆控制稳定性、碰撞安全性都大有裨益。
一般实现车身轻量化会通过这样三种途径:一是应用高强度和轻质材料,二是优化车身结构,三是运用先进的制造工艺技术。我们一一来看。
目前在汽车行业的材料轻量化已经成为一种趋势,在不影响车身强度的情况下,使用更多的铝合金、镁合金、工程塑料等有助于降低车身自重,从而带来更好的燃油经济性。
铝的重量只有铁的1/3,并且回收利用率高,汽车中的铝有85%是可以回收的。但是铝也有很多缺点,比如铝不能够焊接、不容易钣金,喷漆也麻烦,安全性不如钢。
目前,一些厂商只是部分使用铝合金,车身大部分结构还是钢铁的。
最理想的材料当属碳纤维。碳纤维是由化纤和石油经过特殊工艺制成的纤维,除了和一般碳素材料一样具备内高温、耐摩擦、导电、导热等特性外,它强度更高、质量更轻,更耐腐蚀。
碳纤维的密度不到钢的1/4,但抗拉强度却是钢的7-9倍,抗拉弹性也高于钢,在2000摄氏度以上的高温惰性环境中,是唯一强度不下降的物质。
在有机溶剂、酸、碱中不溶不胀,耐蚀性出类拔萃。而且它外形柔软,可加工成各种织物,从使用的角度看,碳纤维不存在腐蚀生锈的问题,比普通金属耐用。
在极端气候条件下,碳纤维的性质几乎不发生改变,使用碳纤维制造车身,可以省去高成本、繁琐的涂装工艺,甚至有人称,碳纤维几乎是目前可知的最能让汽车减重的完美材料。
摸上去手感与塑料差不多,却有着钢铁一般强度和韧性的碳纤维组件,不仅能够帮助整车有效减重,更由于其昂贵的特性而变成奢华的象征。
目前,碳纤维材料在民用量产汽车,尤其是中档产品应用也十分广泛,很多厂商也已经开始碳纤维材料的小组件,如后视镜、内饰门板、空气套件等等。
车身结构优化是通过采用先进的优化设计方法和技术手段,在满足车身强度、模态、刚度和碰撞安全性等诸多方面的性能要求,以及相关的法律法规标准前提下,进而优化车身结构参数,提高材料的利用率,去处零部件冗余部分,同时又使部件薄壁化、小型化、中空化和复合化以减轻重量,最后实现轻量化。
通过CAD对汽车结构布局进行设计,在软件上模拟实体车,然后对整车进行分析,得到零部件的安置情况以及选择合适的轻量化材料,在对整车设计完成以后,可以通过CAE进行进一步分析和运动干涉分析等,使轻量化材料能够达到车身设计的各项要求。
比如激光拼焊板可将不同材质、不同厚度、不同强度和不同表面镀层的板坯拼合起来,然后整体进行压型。激光拼焊板工艺已在汽车领域应用成熟,用于制造车门内板、加强板、立柱、底板和轮廓等部件。
比如对于高强度钢的热冲压成形工艺,是因为在强度超过1000MPa以上时,一些几何形状比较复杂的零件,使用常规的冷冲压工艺几乎无法成形。
目前用无孔性压铸法生产的铝合金大量应用于车轮、进气歧管以及动力转向壳等部件上,由于应用铝材且壁厚减小,轻量化效果显著。
总的来说,汽车车身的轻量化,主要便体现在以上关于材料轻量化、车身结构优化、先进的制造工艺等三个方面。
在现在的汽车市场上,汽车品牌的竞争越发严苛,而汽车的轻量化无疑就是一个十足的卖点,无论是传统燃油车还是新能源汽车,汽车的轻量化都是一直在不断的突破与创新的。我们更应该知道,汽车上每一克的减重,都有着工程师们付出的不懈努力。
文章转载自森蔚汽车