G35项目下横拉杆的对翻孔的同轴度,翻孔直径和孔的圆度是影响装配的重要因素,在整车转配中,以上尺寸不能控制在合理的公差范围内,会出现压出力/压入力不合格,甚至影响整车的耐久要求。采用以往的翻孔工艺,尺寸超差严重也不稳定,给装配带来极大困难。使用优化后的工艺对翻孔进行校形,下横拉杆经过机械性能试验性能良好,为以后类似底盘件的开发提供了宝贵经验。
随着社会的不断发展,人们生活水平不断提高,汽车作为一种日常生活中最常见的交通运输工具,给人们生活带来了便利,与此同时,汽车的安全问题也越来越受到人们的重视,将来的汽车市场,人们会更加看中驾驶安全。汽车底盘件作为车身部件中一类重要的零件,同时承担着整车中,提高汽车各部件的刚性,平衡性,行驶性,安全性的重要作用。汽车底盘摇臂类零件(如下横拉杆,上横拉杆)因为国内外技术水平所限制,公差尺寸很难调整到理想的状态,装车后因为尺寸的误差,经常会出现各种装配问题,甚至后期导致客户投诉,极大影响品牌形象。因此,底盘摇臂类零件也逐渐成为各大公司研究和挑战的对象。研究背景
下横拉杆是我公司承接东风乘用车G35项目中的重要零件,该零件位于新车型底盘区域,主要起支撑车身和减震器,并且缓冲行驶中的振动等作用。由于零件4个翻孔公差-0.2/-0.4,圆度0.2,同轴度0.3;零件材质:FB60T=2.0减薄率小于15%,屈服强度不小于500Mpa;零件试验要求:内外铰接压入力为5KN~25KN,压出力不小于10KN,零件带铰接后需要压入力,压出力试验,需要达到标定的范围值,而铰接的压入压出基本取决于2对翻孔的尺寸精度。而常规冲压工艺,实际零件能做到这么小的公差,难度很大。本次研究的主要目的是如何在原有工艺基础上优化,提升零件的精度。冲压工艺方案
零件采用的技术方案为冷冲压,总共11道工序即:落料,成型,冲孔,翻孔,翻孔,修边,翻边,翻边,侧整形,校孔,侧翻边。由于零件结构的特殊性,很多地方不利于模具结构设计,而零件工序有11道工序之多,每道工序在实际调试生产中会累积很多尺寸误差,到最终出成品,误差累积会更大,而零件的图纸定义翻孔圆度在0.2以内,同轴度在0.3以内,加上其它尺寸,给制造带来极大的挑战。
为解决以上问题,本课题提出一种摇臂类零件的开发经验,为以后开发此类零件提供重要的指导意义。零件简图
图1所示为OP10落料模;图2所示为OP20成型/OP30冲孔/OP40翻孔/OP50翻孔;图3所示为OP60修边/OP70翻边/OP80翻边;图4所示为OP90侧翻边/OP100校孔/OP110侧翻边。
工艺改善:1.零件结构上本身没有一个孔可以用来定位,而成型工序较多。
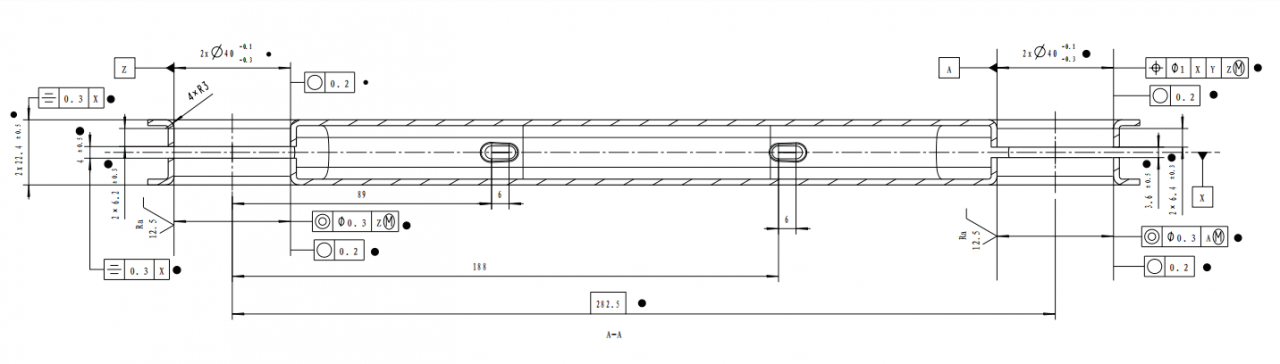
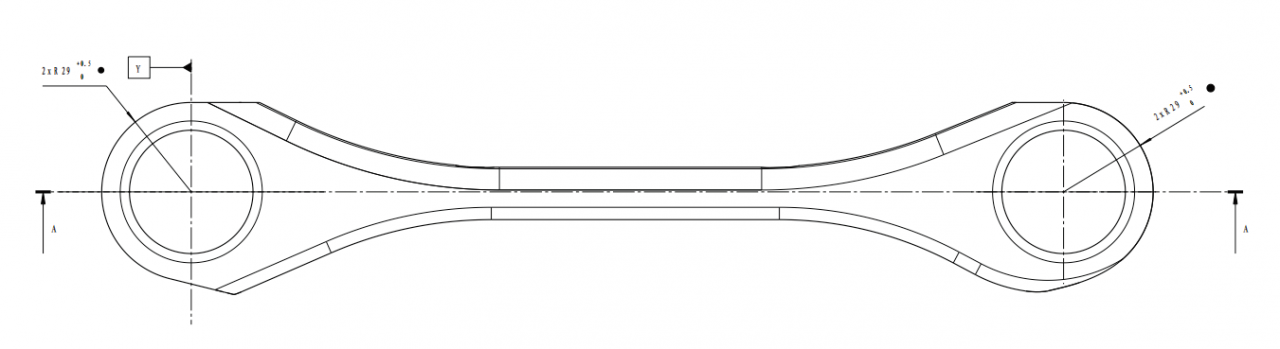
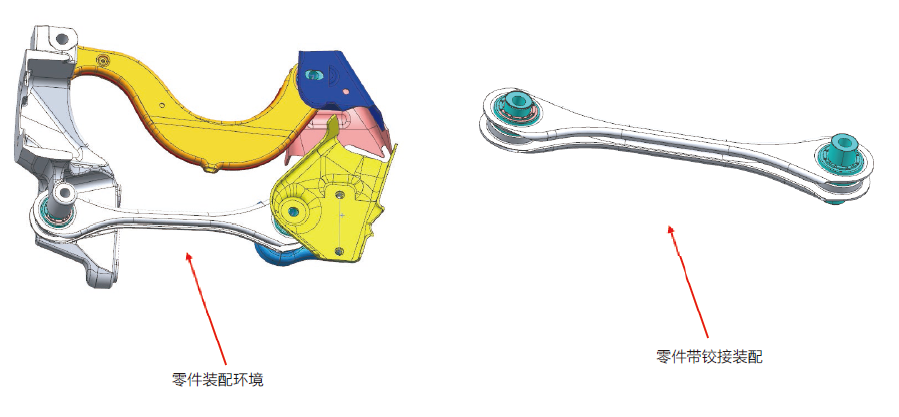
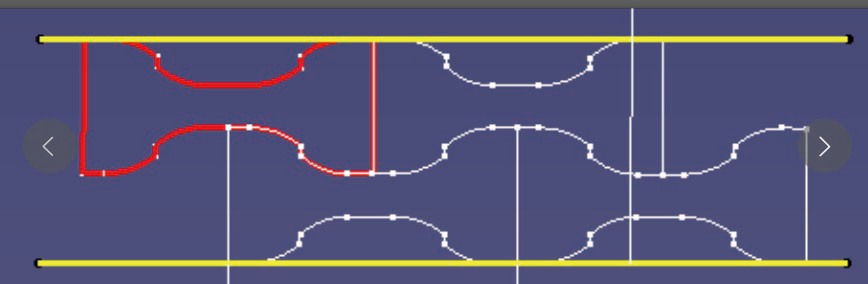
图1
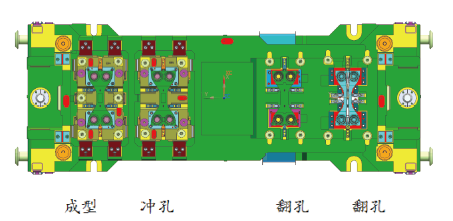
图2
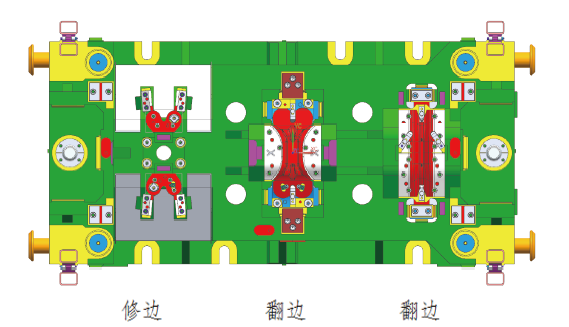
图3
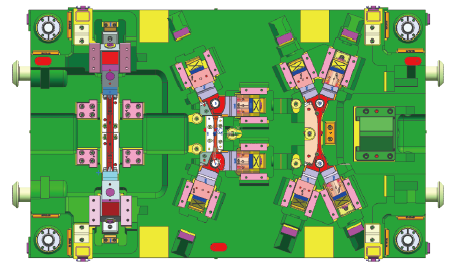
图4
累积误差也会随着工序的增多而加大,开发初期没有很好的工装定位方案,考虑到后期的稳定性,以及量产的稳定性,后期
的调试中调整优化了定位方案。工艺改善:2.OP100增加了校孔工序,此工序通过2对斜楔上的镶块包住翻孔直壁,通过上下翻孔中其中一个孔为基准,矫正另外一个孔的位置,从而实现了上下翻孔的对中,优化了同轴度。

OP10 落料工序增加了缺口和孔使零件定位更加稳定
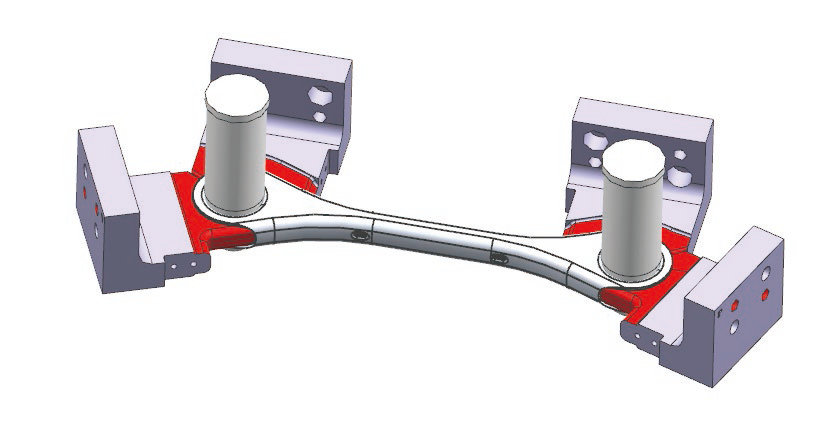
OP100 校孔简图
单个翻孔,孔径要求的公差40(-0.2~-0.4),为了保证翻孔直壁部分能够有很好的垂直度(试验中总结,良好的翻孔垂直度能够有利于压入力,压出力试验指标),在最后的校孔工序中,翻孔冲头尺寸大于前序的翻孔孔径(如前序翻孔孔径39.6,最后的校孔冲头尺寸选择39.7~39.8),这样一来,在校孔过程中,翻孔的壁厚受到一次挤压拉伸作用,直壁部分的光亮带增加,同时也增加了机械性能试验中和衬套的接触面积,对试验效果起到了很大的贡献。同时,对翻孔中的一个孔作为定位,另外一个孔通过以上所述的又一次挤压,矫正了2个孔的相对位置,大大优化了同轴度。结论
调整后的工艺方案和模具结构,对改善零件质量起到了良好的效果,使零件满足设计要求,保证了装配和试验要求,以及零件的稳定性。
通过G35项目下横拉杆研究及优化,累积了下横拉杆等底盘摇臂类零件宝贵开发经验,特别是对于类似对翻孔零件的同轴度如何很好的保证其精度,提供了很好的参考。