汽车外覆盖件汽车车身重要的组成部分,具有板材薄、造型复杂、尺寸大、精度要求高、表面质量要求高等显著特点,具有较大的开发难度,为了质量管控以及成本考虑,汽车外覆盖件成为了主机厂冲压车间主要制造的汽车零件。汽车外覆盖件模具也具有设计制造具有难度大、周期长、质量和精度要求高的特点,具有较大的技术难度,外覆盖件模具导入成为冲压技术领域主要的工作内容。
外覆盖件模具的开发进度对整个新车型项目的进度有着非常关键的作用,是主机厂新车型开发、生产准备中的重要部分。下面从新车型可行性研究到模具终验收的过程谈一谈模具开发流程及各阶段管控要点。
项目可行性判断
通常,产品规划部门依据市场需求、公司发展战略等对新车型开发上市作出规划,针对车型定位、尺寸、生产线、销量、项目大计划等作出规划,形成可研前提下发到各部门进行可行性判断,各相关部门分析判断后形成统一可行性研究报告上报公司决策。冲压领域依据可研前提对生产线通过性、生产模式、模具导入组数、导入周期是否满足等作出判断,形成报告上报项目组,等待车型正式立项。
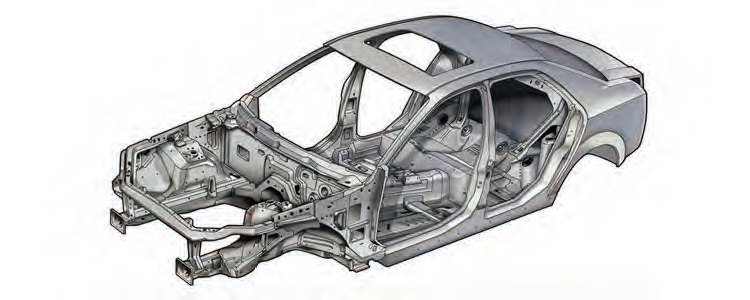
车身覆盖件产品数据发布
项目立项后,车身设计部门依据各领域节点发布产品数模,工艺部门的技术人员根据产品数模进行初步工艺预分析、制造重难点、内外作零件划分、预算判断、招标分包等工作,为模检具招标工作做准备。同时联合采购部门依据项目计划在公司逐层汇报冲压领域模检具详细招标计划。招标过程在此不做详谈,依据公司相关招标流程进行。下面从模检具定标后(即确定各分包零件模检具承制供应商)浅谈模检具开发管理。
冲压内制件制造工艺可行性分析(模具供应商及冲压工艺部门)
冲压工艺部门得到数据后,协同模具承制供应商,对每个零件进行工艺可行性CAE(ComputerAidedEngineering:计算机辅助工程)分析,重点对工序数排布、开暗裂、新特征造型实现性等进行识别判断。提取重点课题反馈车身设计部门进行数据优化修改。
CAE分析的作用:
通过CAE分析,我们可以直观的观察零件板料的成型过程,判断问题产生的原因,预测模具实现的可能性;通过优化设计,最大限度的增强模具工艺性,缩短制造周期,降低制造成本;在铸造加工前预先发现模具和零件的潜在风险点;确保模具的设计合理性,减少设计成本;通过对各零件潜在问题分析,工艺分析部门可及时提出合理的设计变更建议,与车身设计部门共同推进产品优化,更高效的推进开发工作。
模具调试技术员、钳工对零件CAE分析结果进行查看,充分利用现场生产调试的经验,查看调试工艺参数是否正确,拉延工艺补充是否合理,材料流入是否与分析状态一致等进行判断,针对零件的起皱、开裂、钣金质量等风险,及时的提出解决方案。
DL图/CAE的设计与会签
工艺部门得到车身部门最新设计数据后,替换数据再次进行CAE优化分析,之后进行模具DL图设计,多数情况下两者同时进行。
DL图设计(DesignLayout——冲压工序分析设计),也可称为模具工艺流程图,包含:全工序的冲压方向以及送料方向、斜楔的加工方向、各工序的加工范围、各工序的加工轮廓线、基准点与冲压方向的关系、制件加工基准(C/H孔)、拉延模的压料面、拉延筋、预设板材尺寸、工艺补充面、修边模的废料刀布置以及废料流动方向等。同时,DL图还需具体体现相关工序的送料高度、压边圈、压料板的工作行程、板料的定位方式、翻边整形交接刀处理等内容。
DL图设计、CAE分析完成后,需模检具供应商内部完成内部审核,内部审核问题整改完成后即可按照项目计划与主机厂冲压工艺部门进行会签工作,DL图和CAE分析的会签非常关键,直接影响到后续能否在计划周期内正常调试出件以及后期批量生产的生产稳定性。冲压工艺工程师主要审核零件工艺的合理性、生产线的各项参数匹配性、拉延工艺补充的合理性、各工序的成型性能(开暗裂、起皱等)、外观质量、制件回弹、材料利用率等,需依据相关检查表逐项检查。本环节应该关注的重点为工艺排布的合理性以及侧围、翼子板、门内板等深拉延零件的成型性,为后期批量生产的稳定性打好基础。同时有以下两点建议:一是评审时邀请本领域技术专家以及车身领域相关人员参与,针对重点课题各领域共同研究,确认产品优化可行性以及优化方向,提升问题点整改有效性和效率。二是需要检证过往车型同类零件重难点问题点的发生原因以及有效解决对策,及时规避,不断改善进步。
模具结构图设计与会签
依据项目计划,DL图以及CAE分析会签完成,相关问题点得到整改关闭,无影响模具结构设计的课题后,模具供应商根据DL图相关指导进行模具结构图设计,设计软件依据各供应商软件购买情况或使用习惯的不同,采用CATIA或者UG软件进行模具3D结构设计,设计完成后同样先通过内部图纸审核,行评审会签,会签按照相关结构设计检查表逐项确认,确保所有项目满足设计标准要求。
结构设计环节应该关注的重点:一是模具安全性,确保模具起吊、压边圈、压料板、模座等各部件结构强度可靠,特别要防止铸件因为倒角不足应力集中而开裂;二是生产功能性,模具各参数与量产压机相匹配,调试、生产、保养的便利性,重点需要确认含修边、冲孔工序废料掉落情况,废料落料不良会给大批量生产带来极大的困扰。对于评审中发现的问题,应建立明确的评审问题点清单,要求供应商逐项整改到位。部分有争议的课题需要多方进行专题讨论以寻求最佳方案,同时也有必要邀请模具维保现场技术人员、技术专家共同探讨解决问题,特别实在模具整改方面,有时现场技术人员对模具结构提出的优化建议可以帮助有效节省整改周期。
铸造指令发布和泡沫实型制作评审模具结构图设计评审、问题点销项完成后,可进行FMC制作。因FMC与铸件投入均为实体投入,若数据变化较大会造成报废,增加成本以及周期。故FMC制作以及铸造需要主机厂给供应商下发FMC制作以及制造指令后方可进行。铸造指令下发需要产品数据具备一定的成熟度,下发前需与车身、焊装、涂装、总装等相关领域对产品数据进行共同评审,确保数据成熟度,以及铸件肉厚可以吸收正式加工数据的变化量。
FMC制作周期一般需7~10天,制作完成后需要对其进行现场检查以及扫描对比,一是确保与设计模具结构图的一致性;二是检查设计图评审中未发现或不易发现的问题。此过程可以借助蓝光扫描设备进行,提高差异识别精度。
FMC 评审是模具制作过程中不可或缺的过程,因为它是模具结构更改的最后一关,一旦进入铸造阶段,若结构需要较大更改,需要报废重铸,造成周期、成本浪费。
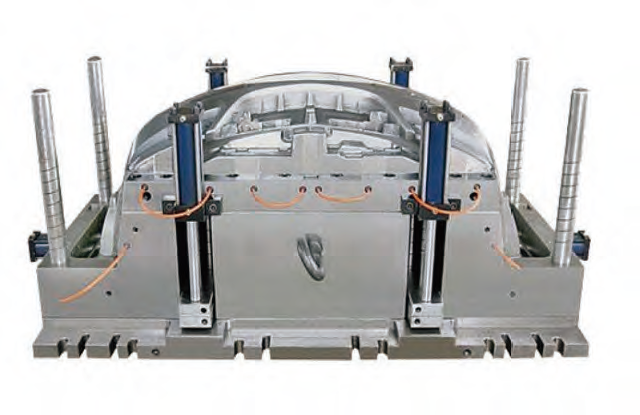
模具铸造
FMC制作整改完成后,即进行铸造,模具铸造周期一般为20~25天,对于全车型模具来说,同时考虑铸造厂排产,铸造周期设置为1个月较为合理。模具铸件在运回模具供应商车间前需要进行铸件检查,主要检查是否有大的铸造缺陷,例如铸件裂纹等,若有不合格部件需及时重铸挽回。其中铸件内部夹砂等缺陷需要在2D加工后才能看出,因此建议主机厂对铸件检查这一环节在模具2D加工后进行。
加工数模发布及模具机加工
模具铸造完成后即可进行机加工,但前提是加工数据已经发布,加工数据的发布同样需要主机厂下发正式加工指令。模具供应商方可可根据产品的加工数据进行数控编程,然后进行模具的机加工,模具的机加工大致可分为:开粗——一次加工——组立——半精加工——(热处理)——精加工等,上文提到的铸件检查在机加工过程中进行,可发现铸件是否有夹砂或裂纹等缺陷,及时对铸件问题进行判断和处理。
此环节还有一个非常重要的工作——精算。精算是控制回弹,保证制件精度、各工序间符型、优化外观品质,保证整车外观光影效果的重要手段,受到越来越多主机厂以及模具供应商的重视,精准的回弹控制可大幅降低后期模具调试周期,精算回弹控制以及模面设计可谓模具供应商核心技术能力。精算需要用机加数据进行,但是为了缩短项目周期,可用铸造数据进行计算,机加工数据发布后对比变化点判断是否需要中重新计算。精算完成后方可进行正常精加工工作。
模具研配、调试、出首件过程
钳工调试阶段包括:模具基准推研——合模到底——带件调试——出件等,模具精加工完成后钳工仍然有少部分转配以及推研工作,模具调试主要检查上下模导向的研合、型面、压边圈、压料板、整形等工作区域的研合,确保模具基础工作到位以及能够冲压出精度、面品合格的冲压件。
模具调试应严格按照调试指导书进行,切不可随意进行打磨拉延筋、工艺补充等修磨工作,从而减少钳工对于技术方案实现的影响。此环节一项重要的工作为首件工艺检证,重点确认工艺方案的实现程度,包括拉延材料流入量、零件减薄、零件回弹、面品、材料尺寸等检证内容,通过不断检证工艺方案,不断优化,逐步提升工艺方案有效性,缩短后期调试、整改周期。同时首件的精度也是衡量各模具供应商技术能力的重要指标之一,可作为后续项目招标的重要技术能力依据,有利于增强各模具供应商竞争力,不断优化选择技术实力更强、成本更优、制造周期更短的模具承制供应商。
模具预验收
按照项目制造管理计划,模具供应商工艺检证完成,对不合格项目完成整改达成预验收条件后,可向主机厂工艺部申请预验收,模具供应商需要提供模具的自检报告和零件精度、面品等质量报告,主机厂工艺部在接到模具供应商的预验收申请后,组织人员到模具供应商进行预验收,验收人员因包括工艺技术人员、现场模修人员以及质量检查人员,主要从模具动态、静态、冲压件质量三个方面严格按照检查表进行模具验收,冲压件质量应包括精度(关键精度)、外观品质、减薄、翻边质量等几方面综合评价,同模具动、静一起输出详细问题点清单,便于后期模具供应商以及驻场人员进行销项推进。
模具预验收完成后,便可依据项目回厂调试策划以及预验收模具状态,与供应商制定详细问题点整改计划,确认模具回厂时间。在预验收过程中发现的问题需在供应商工厂内整改完成后,方可通知主机厂人员进行验收复检,复检后精度、面品、问题先销项达成模具回厂条件后,收到主机厂发模通知,方可打包发运。
模具主机厂调试与验收
模具到货后,在主机厂的工作主要有模具点检——生产线参数匹配——厂内外差异对比——模具基础工作恢复优化——精度/面品提升(整车匹配)——生产效率提升——量产——模具终验收等几个阶段,整个模具调试的周期一般在4.5~6个月。
模具供应商内调试过程中主要有一个几个方面需要重点关注:一人员方面:模具调试初期,交模人员起着至关重要的作用,在调试期间,需协调供应商派出一名调试技术专家以及2~3名动手能力强钳工全程参与调试,好的技术方案以及动手能力强钳工可以有效提升整改有效性以及降低整改次数,从而缩短调试周期,保证项目进度。
管理方面:因模具调试周期只有不到半年,同时整车装车数量以及时间有限,因此,在调试期间需要把握各阶段的整改重点,同时需要制定详细的月计划、周计划以及每日的整改、模具上机计划,同时要保证留有一定的工序件,以便随时可以查找、判断问题点的原因,整改对策等,确保问题点可以按计划快速整改到位。
整车匹配:归根结底,冲焊涂总四大工艺都是为整车品质服务,调试期间,除了保证冲压单品精度合格外,也需要对整车装配关键部位精度进行重点管控,有时也需要配合整车品质进行配合性公差偏置整改,需要具备一定的精度解析经验以及装配尺寸链等知识。
经过调试,车型量产以及模具问题点、零件精度、面品、生产效率、模具故障率等各方面指标达成验收条件后方可进行终验收,完成终验收后,模具的开发工作才算阶段性完成,交付制造现场进行日常生产、点检保养和故障维护。随着车型销量变化、改款、车型换代等,产量逐渐减小,直至车型停产,车型停产后模具仍需保留15年,以备SP件生产,15年后模具报废,回炉重铸,从而完成模具整个生命周期使命。