厚度2.02mm贯通式门槛辊压件为左右纵梁加强板,使用材料HCT1180X+ZG10/10,处于A柱与C柱之间,零件长度1759.5mmm。HCT1180X+Z钢板属于超高强度钢板,其材料抗拉强度达到1196MPa,屈服强度933MPa,延伸率≥4%。压成型工艺是卷料通过多组不同的截形的辊轮连续轧制得到所需要的零件截面形状的工艺,通过纵对纵梁加强板开发过程中的研究,为以后同厚度高强板辊压件的开发提供了宝贵经验。
由于节能减排的需要,汽车的轻量化的局势越来越紧迫。实验证明,汽车质量降低一半,燃料消耗也会降低将近一半,相应排量也会根据燃耗减小。
为保证汽车强度和安全性能,汽车轻量化必须在保证结构强度的条件下降低零件重量的条件下达成。近年,国外大型汽车厂商所开发的新车型中,辊压型钢零件已占比超过60%,辊压门槛在国内合资品牌厂商应用也逐渐普及,辊压件减重在汽车轻量化中也是不可或缺的,相比传统冲压件焊接总成,辊压成型工艺减重甚至能达到50%。
研究背景
1180Mpa级厚度2.02mm辊压件的开发应用项目依托于新车型E43-PHEV项目电动车产品开发,该项目辊压零件左/右纵梁加强板较以往辊压件使用的材料,强度高,延伸率更低,料厚也更厚。

零件形状如下

零件截面图

零件俯视图
CAE分析
通过COPRA软件进行CAE分析,得到辊压件卷料宽度为236.3mm,辊压成型工艺卷料宽度公差较高,一般为-0.2~0mm公差带,过宽会使条料边沿挤压到辊轮内壁产生锌皮碎屑甚至使醒面挤压变形,还会产生巨大噪音,过短容易产生折弯角度不良。其辊花图如下:
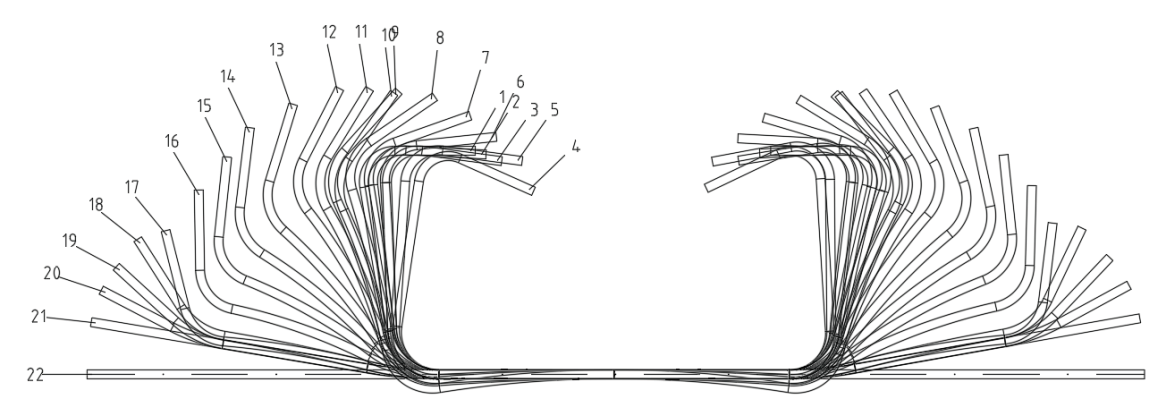
辊花图
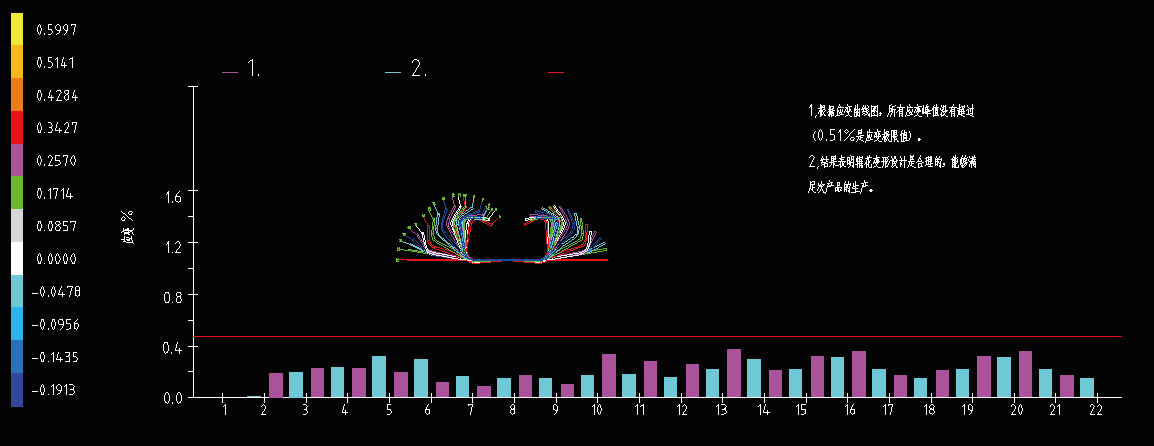
应变分析
通过CAE分析结果可得,根据数据应变曲线图,所有应变峰值没有超过(0.51%为应变极限),结果表明辊花变形设计是合理的,能满足产品的生产。
工艺工序
纵梁加强板零件左右件完全对称,即辊轮工装使用一套即可。该零件成形过程中回弹量大,回弹角度补偿角度超过20°。
工艺过程如下:
开卷——校平——冲孔修边——21段辊轮成型——1段辊轮整形——1段辊轮矫正——切断——检验装箱。

切断位置
零件切断形状如图所示,步距1785mm,计算得到材料利用率达到92%。
实际开发
圆角开裂
前期回厂材料延伸率为5%,上线后状态如下图所示。

上线开裂
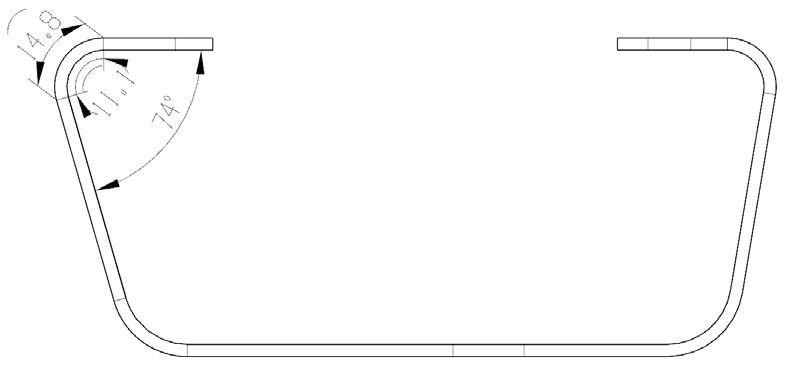
截面弧长
根据中性层计算方式:中性层弧长L=π(180°-74°)/180°×(6+2×0.41)=12.617mm
则外弧线延长率ɑ=(14.981-12.617)
/12.617×100%=18.74%;可得材料延伸率不满足外弧长延长率。
解决方案
要求更换延伸率在7%的材料进行调试,零件外R开裂减小,但仍会偶尔出现。
为彻底解决开裂问题,设计通过将零件上R大小由R8改至R9,并加大辊轮上下轮折弯间隙零件外R不再开裂,如下图。此时固化材料供应商生产参数,保证量产后材料性能。

外R 不再开裂
R边沿裂纹
由于切断工装不能一次性切断纵梁加强板,需要在辊压前工序冲孔进行局部预切,如下图所示。2.02mm厚度高强板修边光亮带极小,由于板料冲裁方向向下,辊弯方向朝上,使得毛刺带在R外沿,弯曲时极易产生撕裂。
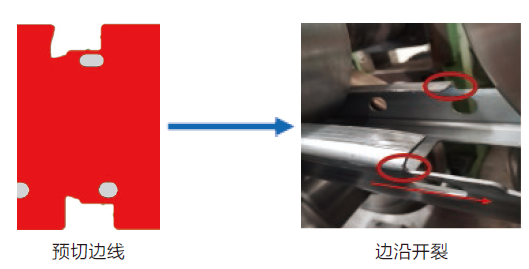
解决方案
通过增大冲切位置R角的过渡圆弧大小,减小弯曲时内外弧的长度比,使外沿部分减小延伸率,从而使得外沿不再发生裂纹,如下图所示。
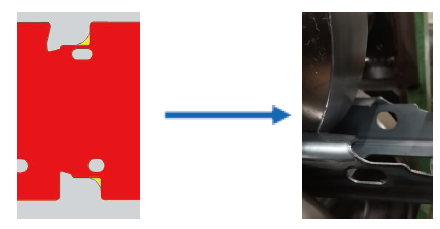
法兰折弯回弹
从下图中可以看出,零件法兰边全部向上翘曲,这是由于实际生产过程中,上下轮的间隙未调至合适大小,辊轮未给予足够的折弯回弹补偿量。通过合理调整辊轮间隙,根据辊花图布置校形和整形工序,最终将零件回弹予以消除。

法兰边回弹

回弹补偿
纵梁加强板相对于以往辊压件来说,其特点就是材料延伸率低,材料厚,这就造成零件在折弯过程中特别容易产生开裂。左右纵梁加强板零件单边重量6.19kg,整个侧围门槛部位总成仅由7个子件焊接,大大减少焊装工序和门槛部位总重量,零件的减少也就意味着工装投入的减少。很好的顺应汽车轻量化的发展。
结论
1.零件采用辊压件形式进行设计,材料利用率达到92%以上,这是普通冲压零件普遍无法达到的材料利用率,大大的减少了材料的浪费。
2.纵梁加强板零件设计成1759.5mm长,贯穿AC柱之间,减少普通纵梁设计时产生的多个零件焊接工序,大幅度减少了工装的投入和中间工序,节约成本。
3.纵梁加强板左右键截形一致,辊轮工装左右通用,减少辊压成本的投入。
4.将纵梁直接设计为一个零件连接前后柱,减少了焊接工序,从而减小了累计误差,提高整车精度。
通过减少焊接工序件的设计,减小整车重量,降低油耗,实现轻量化发展。