一用户友好型操作模式
目前,汽车行业为大规模生产电动汽车而加紧步伐,世界各地涌现出大量新工厂,全部配备了高端技术,并准备以最快的速度提高产量。通常,这些工厂不得不依靠新雇用的劳动力,而新员工也面临着大量不同的生产机械控制系统,这影响了工业用操作界面的设计。然而,最重要的是避免恼人的复杂设计:便于操作的生产机器能够创造真正的竞争优势。事实上,简便的设计能惠及所有人:它能催生许多新技术,清除错误并减少培训要求。
使用工业界面的是一个广泛的群体——这一群体中包含实验室工程师、工厂操作员和工厂主管等,但他们中的每一个人都需要能够正确操作设备来执行工作任务。简陋的智能手机证明了这是一个现实的目标,而通快正是选择了这种菜单导航形式作为典范。
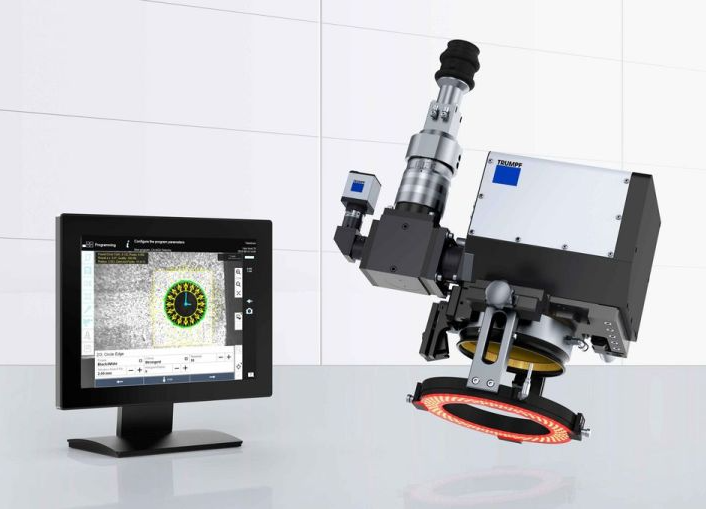
图 1_VisionLine
简易至上
即使是没有任何基础知识的首次使用者也能凭直觉理解智能手机的基础功能,如拍照或打电话。遗憾的是,对于那些操作激光加工系统的人来说则不同。通常情况下,菜单导航很少会对自身进行解释,最多会让用户参考用户手册。同样,它也缺少防止错误操作的提示信息(“您真的要……吗?”)。如果用户想要开发一个新的定位,他们需要自主思考整个过程。正是在这些考虑下,通快的开发者们设计了 VisionLine 定位传感器的界面。它具有一个基本的垂直向导,为新工作的设置提供逐步的支持。它还包含了一个结构清晰的水平菜单,其中包含很多细节,使用户不可能遗漏任何一个步骤。最后,整个设置会自动保存在一个默认的名称下。即使是那些没有图像处理知识的人,也能通过 VisionLine 界面快速轻松地取得成果。二自动传感设置
传感器越发复杂,它们的使用却变得越发简单。
确定合适参数的过程涉及思考、经验和普通试验和错误的组合。然而,一旦有三或四个值在发挥作用,这种方法就会到达它的极限。这时我们就会发现我们身处一个不对称、多维度的参数空间。特别是电动汽车领域使用的制造工艺需要能够处理这种复杂的测量任务的传感器。
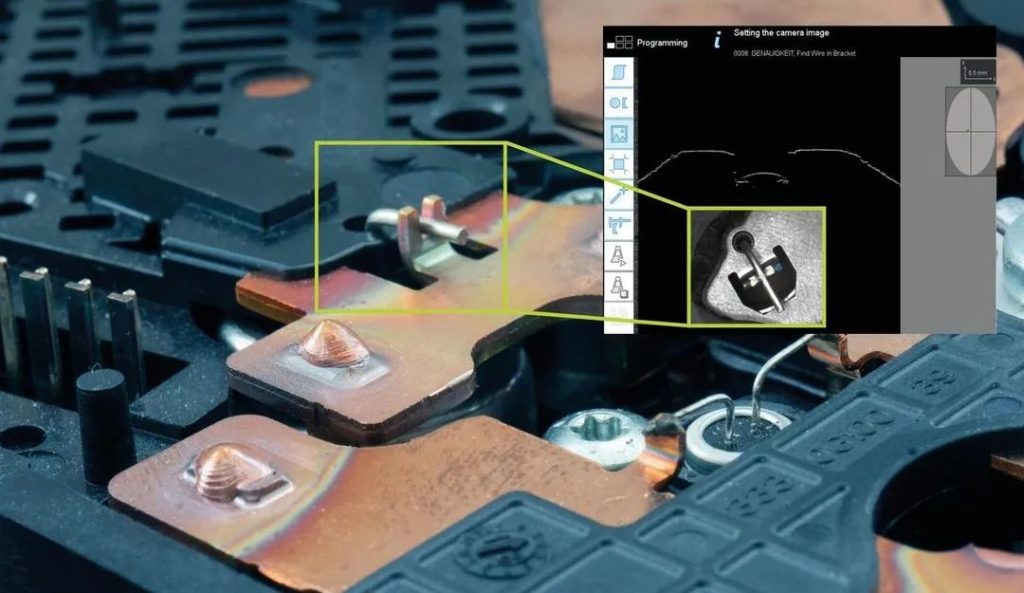
图 2_OCT sensor
需要一个绿 A 快捷键
以 OCT 传感器的图像调整为例,这些传感器用于监测定子上的扁铜线焊接或安装在控制单元中。OCT 传感器出现图像问题的原因有几种:轮廓线可能被打断,多重反射干扰图像,线条褪色或干脆消失,结果图像质量不够好而无法提供令人满意的测量结果。这就意味着评价软件无法确定焊缝是否位于正确的位置或拥有足够好的质量。所以,如何制造一个清晰的图像?类似一个高质量的 SLR 照相机,OCT 传感器拥有能够手动设置的参数:曝光时间、阈值、频率、缩放系数、参考值等等。总共有 22 个参数,在某些情况下,有数百个等级。在这 22 维空间的某个位置有一个点,在这个点上所有 OCT 参数都能根据当前的组件位置实现完美地设置。
通快采取了同样的方法,并且在所谓的进化算法的帮助下,通快为 OCT 传感器创造了一个绿 A 快捷键。这在更小的规模内完成了自生命出现以来大自然一直在做的事情:自然让个体相互竞争,繁殖,随机变异,并始终在观察会发生什么。经过了数百万年的进化,这产生了不同生物,如孔雀。幸运的是,对于 OCT 算法而言所需要的时间少得多,仅 15 秒。
生存之战
22 个 OCT 图像参数的每个随机集合会构成一个个体,然后在这个参数集的基础上产生一个图像,通快开发的评估程序会对其进行检查,以确定该参数集在其自然环境中的“生存”情况。下一个随机参数集进入竞技场,以此类推。参数组中最合适的一组将“繁衍后代”并将各自的优势组合在一起传给下一代。然后,这种进化的游戏重启,周而复始经历多代。然而,如果以这种方式继续下去,这将造成越来越多极端或者容易出错的“后代”:参数值将倾向于局部最小值并最终陷入进化的僵局。因此,每隔一段时间,该算法就会让它们在一定范围内随机变异。这为进化的过程重新带来了活力,并带来了新的组合可能性。
最终,它产生的参数组合是任何人都无法设计出来的——某些情况下,其数值能定义到小数点后几位。使用 OCT 传感器的操作者仍然对所有个体参数集的“生存斗争”并不知晓。对于操作者来说,只需要点击按钮等待 15 秒,进化过程就结束了,系统也会针对当前的组件位置提供最佳的相机设置。三自动参数化
该传感器在未能检测到废品和急需后续处理之间引导了一条路线。
电动汽车制造商目前正面临着一个困境:激光焊接通常仅在最后阶段使用,此时一个零部件已经基本完成,比如一个电池或定子。换句话说,在激光焊接时发生的一个错误将意味着整个零部件被退回或返工,可能会造成较高的代价。另一方面来说,没有比反应过度的传感器不断报告错误更糟糕的了,因为传感器视野中可能有上百个被测量的接缝间距,不可能每一个都绝对合适。考虑到电动汽车行业的产量,即使是百分之一的后续处理率也会使整个过程陷入停顿。在这种情况下你需要后退一步。毕竟就像在日常生活中一样,在制造业工作不需要成为一个完美主义者。有时,”差不多 “就是足够好。
这是通快铭记在心的一个教训。VisionLine 或 SeamLine Pro 等传感器系统用于监测一系列的部件属性如接缝间距,并相应地调整系统参数。这能帮助生产经理在无法检测到废品和迫切需要后续处理之间找到解决方法。传感器技术的最新趋势是主动 g 过程逻辑(APL),这就是能把废品变成一个完好部件的原因。
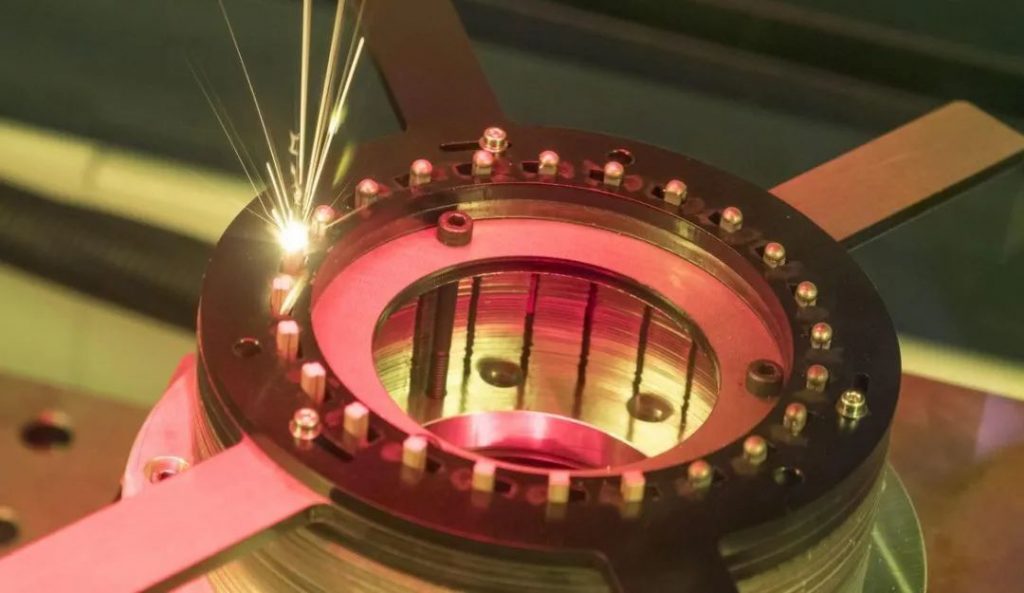
图 3_Online Seam Control
足够好
APL 根据开环控制的原则运作。对于一个需要 200 次焊接的部件,传感器在每次点焊前测量接头间隙。如果有必要,传感器系统会根据测量结果调整这个特定点的焊缝。例如,如果传感器检测到两根要焊接在一起的铜棒之间的水平或垂直方向上的没有对齐,它就会调整激光系统和激光能量,降低速度,命令多焊两道或焊不同的图案等。
无论是标准焊缝还是不寻常的焊缝,用户都可以通过实验室测试哪种方式能获得 “足够好 “的结果。这些数值随后会被记录在一个表格中,传感器软件在每次测量时都会查阅该表格,以提取基准值。这种基于 APL 的上游质量保证已成为电动汽车行业的标准做法,它有助于消除废品并大幅提高产量。与上述两个趋势(用户友好型操作和自动传感器设置)一样,其他行业现在也发现这种新技术可以帮助他们缩小生产力上的差距。