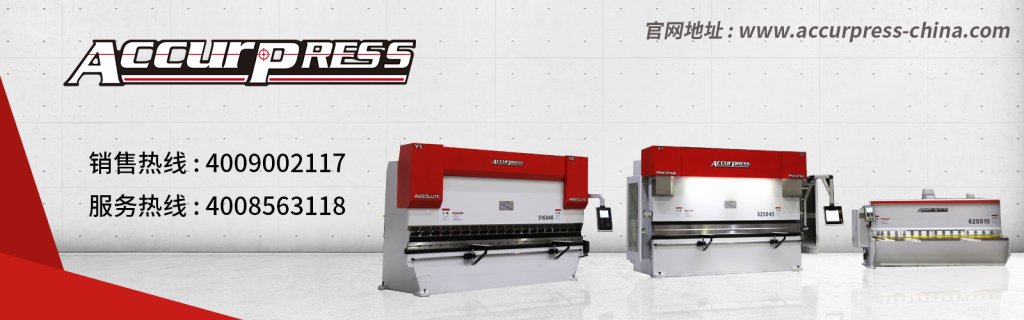
来源 | 期刊《汽车工艺与材料》
摘要:为提高白车身零部件焊接柔性化、自动化程度,快速实现车型导入,将模块化思维应用于零部件产品焊接工艺开发中,通过对白车身连接工艺分类重组,结合柔性化焊接技术及工装夹具快速切换技术,最终实现零部件焊装线快速适应多类产品的焊接要求,同时显著提升设备利用率。
关键词:柔性化 模块化 白车身零部件 焊接工艺
01、前言
随着汽车制造技术水平的高速发展,各汽车主机厂焊装工艺的自动化程度越来越高,其中机器人的投入使用带来的自动化提升最为明显,为适应主机厂的发展,为主机厂提供焊接零部件的供应商也开始大量使用机器人进行自动化生产,节约人力成本的同时,提升自动化率,提升产品质量的可控性与一致性。
同时,随着生活水平的提高,人们对汽车的需求越来越多样化、个性化,促使汽车制造向高柔性化方向转变。焊接零部件供应商为适应这种需求,也在寻求更为经济,更高效率的柔性生产方式。
02、白车身零部件焊装工艺模块化
由于零部件供应级多为白车身分总成,产品种类、平台的不确定性导致很难以车型平台的划分定义生产方式,同时主机厂对零部件的需求量是根据市场而变化,考虑生产经营因素,零部件供应生产线要求进行满负荷运转,实现经济效益最大化,所以在一种车型零部件需求下降时,需要立即补充其它车型零部件,维持生产持续进行。
针对以上情况,提出以焊接工艺进行模块化设计,配合夹具切换技术,设计不同工艺的功能站,抛开车型及产品平台概念,对同种工艺的产品集中生产,既提高了设备的利用率,同时可在产量变化时,随时补充相同工艺的任何零部件,使生产线产量不因某种产品需求变化而随之改变。
2.1 柔性点焊工作站
白车身最主要的链接工艺是电阻焊,一般占整车焊接当量60%以上。电阻焊中点焊使用最多,尤其在白车身零部件中使用更为广泛,可以说,实现点焊的模块化、柔性化工艺,即可实现白车身零部件的柔性化焊接生产。
根据白车身的结构特点及节拍因素,点焊工作站可模块化设计成以下几种形式,满足不同节拍,不同产品的需求。
2.1.1 对称零件点焊工作站
白车身大多数零件都是左右对称结构,例如左右纵梁、前后门等,图1 所示为左右前纵梁零件产品图,对于这类对称结构的焊接件,设计对称料口式焊接工作站(图2、图3),机器人焊接左右对称的零件,焊枪等通用性更强,焊接轨迹对称导入即可,在节省设计成本的同时,生产也更好管理。
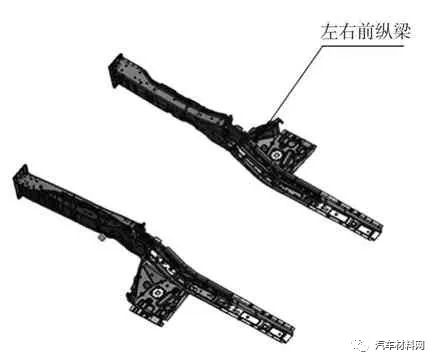
图1 左右前纵梁产品示意
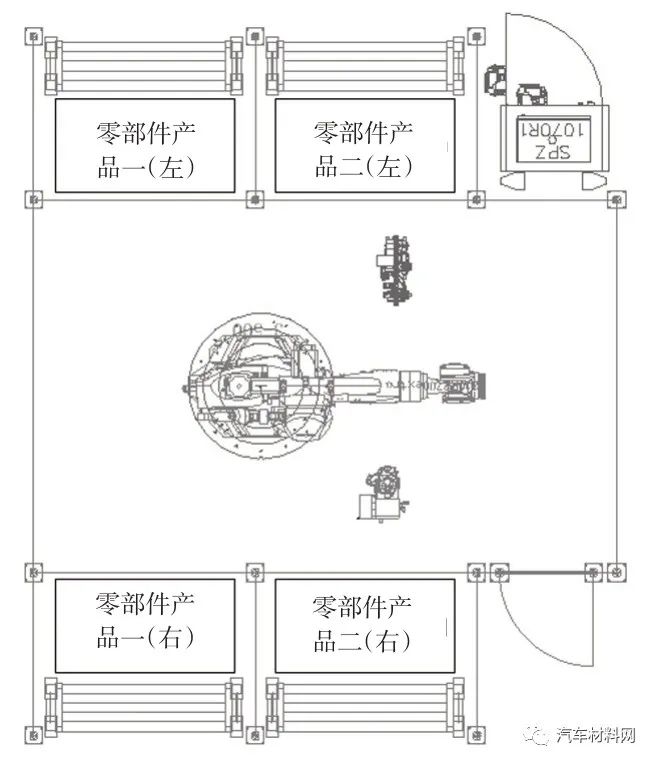
图2 对称零件点焊工作站
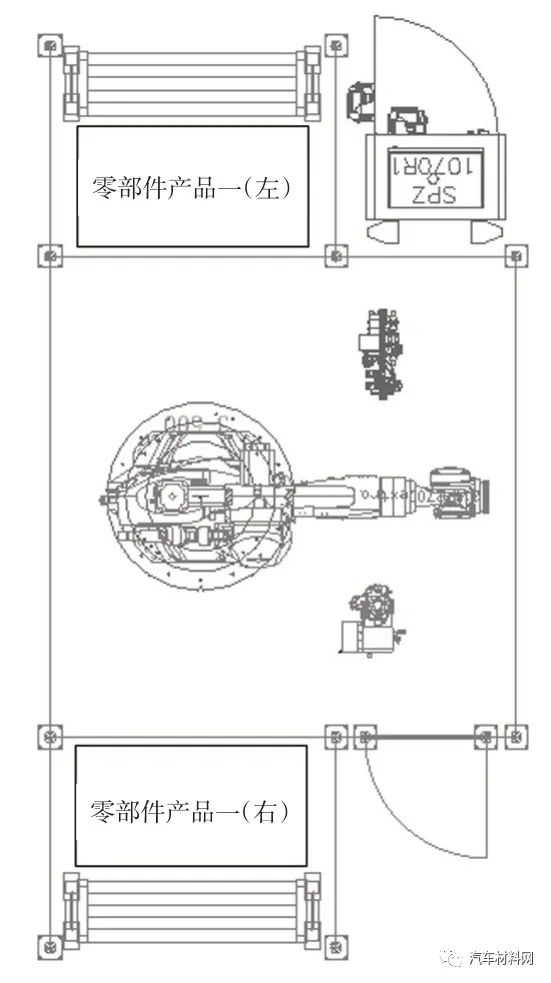
图3 对称零件点焊工作站
2.1.2 非对称零件点焊工作站
例如前围、包裹架、中通道等零部件为单一零件,图4 所示为前围档板总成产品示意,对于这类非对称结构的焊接件,焊接工作站可以设计成如图5 形式,单侧上下序进行焊接,方便零件在工序间的传导及物流管理。
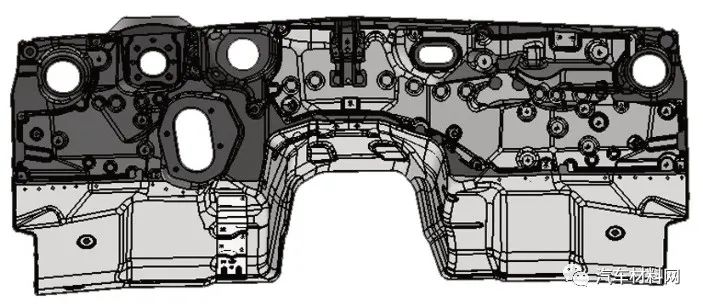
图4 前围档板总成
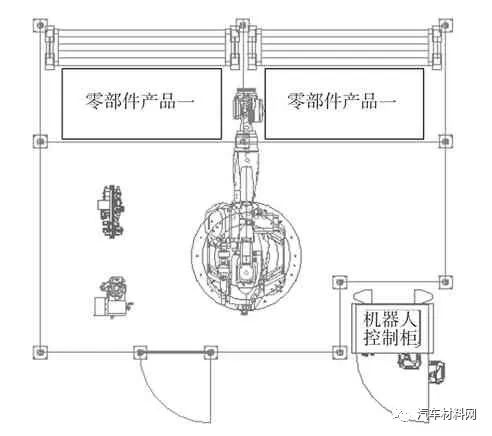
图5 非对称零件点焊工作站
2.1.3 随行点焊工作站
例如三角窗、门槛以及层级更深的零部件,由于焊点少,机器人如果焊接单一种类零件,利用率低,因此设计随行点焊工作站(图6),利用机器人七轴增加机器人工作范围的方式,使一台机器人对应多个料口,多个零部件的焊接,提高机器人的利用率。
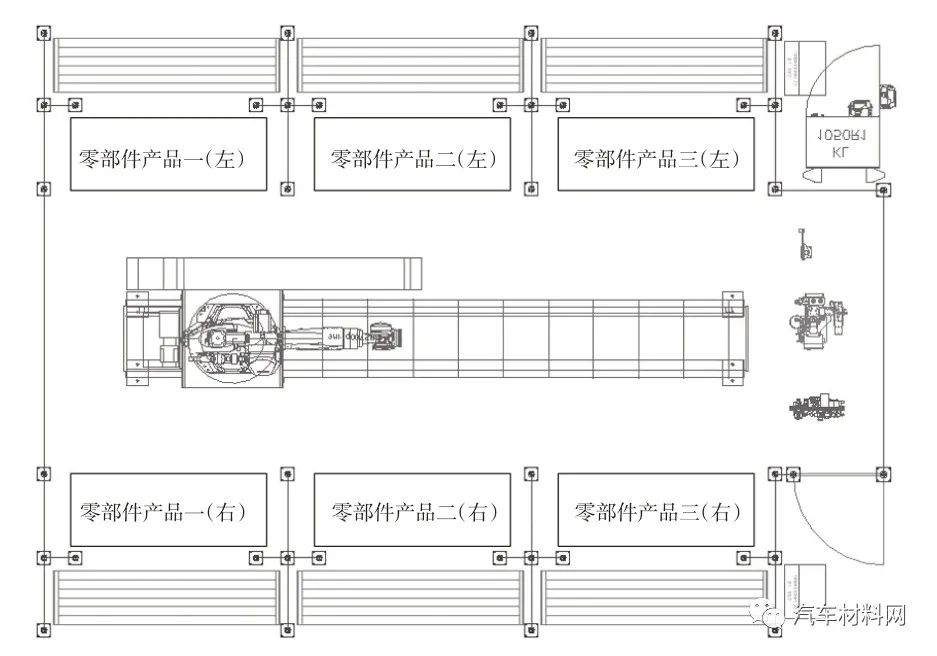
图6 随行点焊工作站
2.2 柔性二氧化碳焊接工作站
除电阻焊之外,二氧化碳气体保护焊也是使用较多的连接工艺,而且由于气体排放的严格要求,一般需要建设二氧化碳焊房工作站,配备独立的排风系统(图7)。
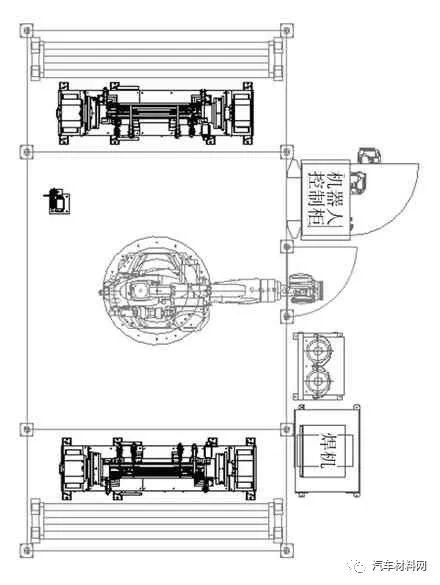
图7 二氧化碳焊接工作站
二氧化碳焊接工作站需要设置变位机,适应二氧化碳焊道分布不均衡现象,同时提高不同产品二氧化碳焊接工艺的柔性化。
图8 所示为常见零件二氧化碳焊道位置图,图中标识圆圈内分布数量不等的二氧化碳焊道,可见该纵梁端面360°内4 个面均有焊道,为保证机器人二氧化碳焊接可达性及焊接角度可选择性,最终达到优质的二氧化碳焊接质量,需要变位机设备,在机器人姿态不可达时,机器人控制变位机,转变产品角度位置,实现焊接,并且变位机的非工作面可预留后续产品的夹具位置,在不同产品工装混流性差的时候,变位机的存在提高了工作站不同产品柔性的可能性。
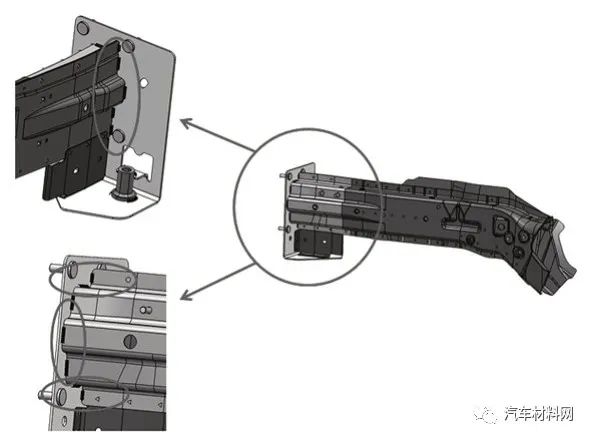
图8 二氧化碳焊道位置
对于白车身零部件连接工艺,多数由点焊、二氧化碳气体保护焊、胶粘、凸焊等组成,胶粘、凸焊目前在白车身零部件供应中使用较少或多为人工手动形式。
上述模块进行尺寸约束,以工作岛式的形态建设,同时可以连接成线,随意组合,由同一套控制系统进行生产控制管理。如图9、图10 所示,自由组合拼接而成的生产线,多见于前后纵梁、前围档板等多工序完成的产品总成,设计者只需合理分序,组合工作站,即可快速搭建生产线。
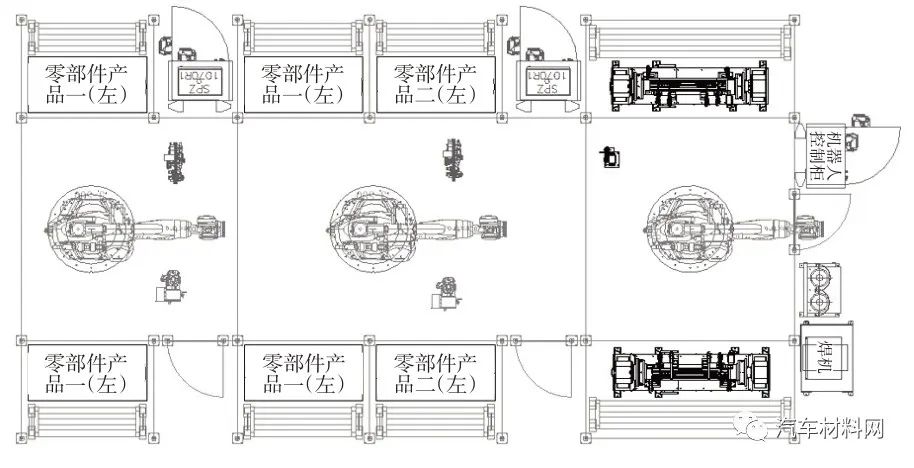
图9 对称结构零件生产线
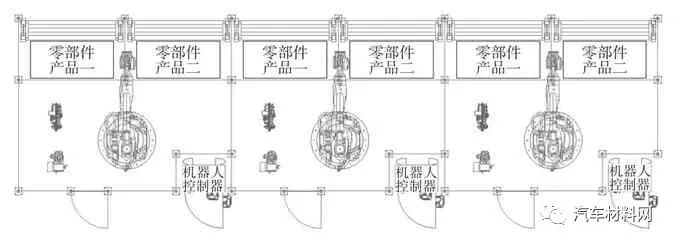
图10 非对称结构零件生产线
03、夹具切换技术
区别于主机厂生产线,夹具切换多采用转台、转鼓、滑台等设备,切换柔性化能力有限,而且设备价格昂贵。为使模块化工作站适应不同产品,打破产品平台化限制的需求,零部件焊接需要使用柔性化更高,性价比更高的夹具切换形式。
下列夹具切换形式,可与零部件焊接工作站配合使用,快速切换夹具。同时焊接工作站的料口标准化及夹具库的使用,可实现零部件生产无车型限制的目标。
3.1 夹具快速切换形式1
如图11所示,夹具基板下部与料口定位机构设计对应的销孔配合结构,通过导向使夹具能够准确落位,利用销孔的配合关系保证X、Y方向位置精度,靠自重落位到Z向定位面保证Z方向的位置精度。
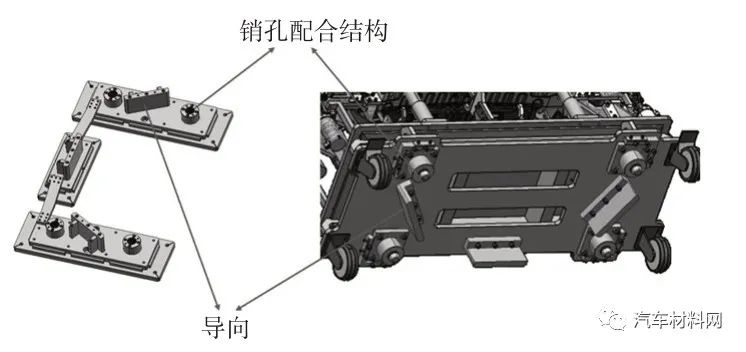
图11 夹具快速切换形式1结构
由于该机构需要Z方向垂直落位,将夹具落到料口定位机构里,所以夹具切换时需要设备将夹具举升及落下,一般生产中可以使用手动液压搬运车进行夹具切换和转运,如图12 所示。
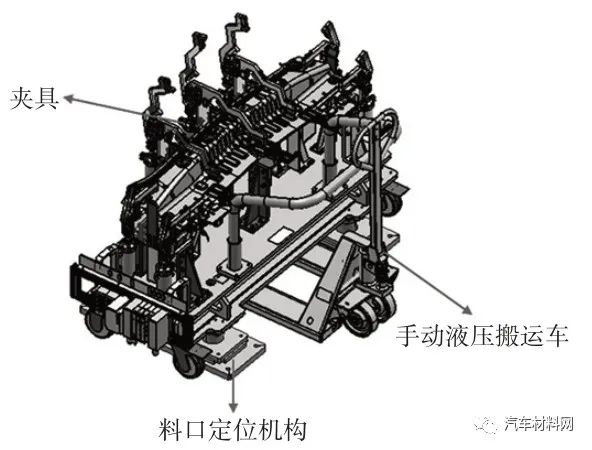
图12 利用手动液压搬运车切换夹具示意
此夹具切换形式结构简单,料口标准化程度高,成本较低。但同时定位精度及切换夹具操作性不高,只适合应用于零部件点焊工作站使用。
3.2 夹具快速切换形式2
如图13 所示,定位原理与夹具快速切换形式1相同,区别为形式2 由料口定位装置自动对接夹具定位孔,并举升夹具,在Z方向进行定位。
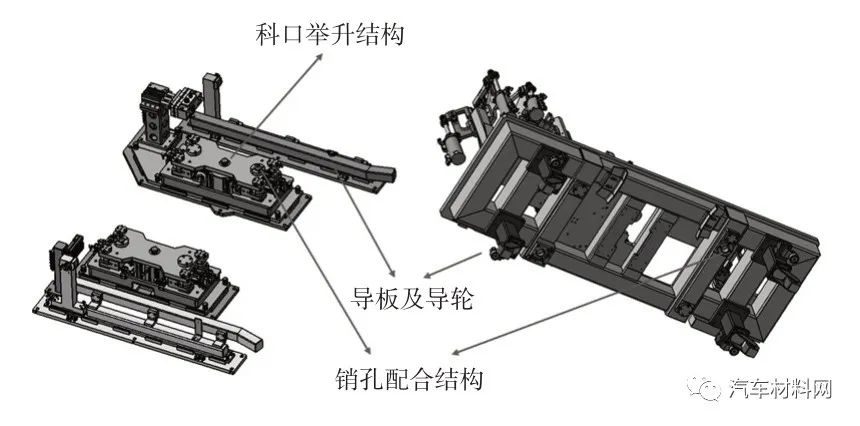
图13 夹具快速切换形式2结构
此夹具切换形式操作简单,人工直接将夹具推到料口位置,信号确认后由料口举升机构自动对夹具定位;缺点是料口机构较复杂,举升机构需要定期校准维护,保证夹具位置精度。同样只适合应用于零部件点焊工作站使用。
3.3 夹具快速切换形式3
使用滚珠与导轮定位形式保证夹具切换后的位置精度。如图14 所示,水平滚珠支撑夹具,在Z向起到定位作用;夹具导入过程中,依靠侧向滚轮与侧顶气缸保证X 向准确定位;在工作位置,料口内侧设计两组夹紧气缸固定夹具,同时进行Y向定位。这样X、Y、Z 3 个方向都完成准确定位[1]。
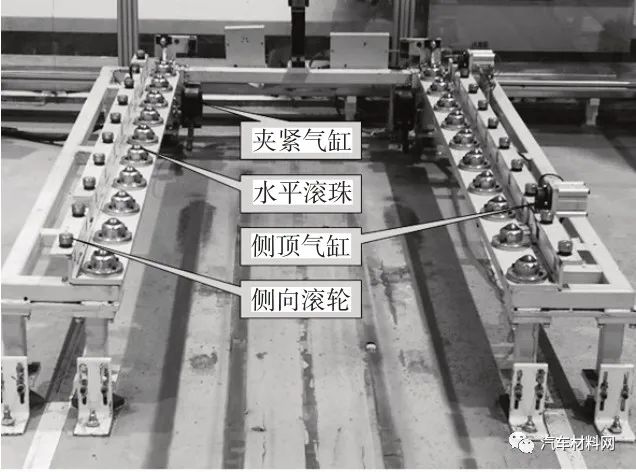
图14 夹具快速切换形式3结构
此夹具切换形式结构复杂,成本较高。但夹具的X、Y、Z 3 个方向都进行了精准定位,位置精度高,适用于点焊、二氧化碳焊、螺柱焊等所有工作岛使用。
上述3 种夹具切换形式均可由AGV 替代人工,实现自动切换夹具,形式1 需要与潜伏式AGV配合使用,形式2、3 与一般牵引式AGV 配合即可。使用AGV 切换自动化程度更高,配合夹具库按生产计划切换夹具及生产车型,线体可升级为自动化高柔性零部件供应生产线。
04、焊装工艺模块化优势
开发设计多种焊接工艺模块工作站,只关注工艺内容的实现,打破传统生产线以车型平台建线思路,可以更好地融入不同车型零件的生产,时刻保持生产线设备的利用率,同时可以更便捷地增产提速,快速响应产能变化需求。
a.可增可减,适应性强。工作站的生产方式,可以快速适应产能变化及解决空间对生产的限制。当产能增加或减少时,可以通过关闭或快速复制工作站方式快速应变,关闭的工作站安排其它零部件生产实现经济效益。如果场地面积受限,可以将工作站建立在不同位置,利用一切可利用的空间,通过物流转运实现工艺的连续性,规避了整线建设对大空间的硬性需求。
b.模块设计,精准快捷。将上述工作站进行模块化,当需要建设生产岛时,直接调入工作站模型,进行必要的产品分析、焊点分配及仿真验证,即可完成全部的开发设计工作,其它设备数量、选型、平面设计等直接调入模块内容,大大提升了设计效率及准确性。
05、结束语
着重介绍了模块化设计理念在汽车零部件焊接工艺中的应用,结合零部件厂商的生产模式特点,提出几种实用的焊装工艺模型,通过模块化工艺,配合柔性化的夹具切换技术,可以很好的实现当前自动化、柔性化的生产要求。同时模块化设计提高了设计质量和效率,缩短了焊装生产线的开发设计周期,利用工艺模块化的有利条件,可以开发更多的汽车焊装工艺功能模块,将模块系列化,应用于更广泛的场景中,发挥工艺模块化设计的最大优势。
参考文献:
[1]李磊,于慕寒,刘菁茹,等.AGV在汽车焊装工艺中的应用[J].汽车工艺与材料,2020(12):52-58.