针对7 0 7 5 – T 6 铝合金和6061-T6铝合金,挑选电阻点焊以及自冲铆技术进行了实验研究。分别设计3组试验,涉及同种。
材料以及异种材料的连接,并观察连接后结构与形貌,测试连接强度。结果表明,6061具有良好电阻点焊已经自冲铆性能;7075电阻点焊性能差,针对7系铝合金连接工艺的选择,尽量避开类似电阻点焊这样过度加热的工艺方案,SPR连接工艺要求下层板要采用较高延展性的材料,延展性差的材料只能放在上层,7075应用自冲铆技术时,只能作为上层板。
在政策性引导,OEM 不断追求,以及环保、法规等方面要求下,汽车轻量化是领域内共同努力的方向。汽车轻量化是在保持汽车原有的性能不受影响的前提下实现汽车重量的减轻,主要通过结构优化、轻质材料的替代应用、制造成形工艺的升级以及先进连接技术的应用等四大途径来实现。
白车身的重量占了车身总重量四分之一以上,现在汽车车身一般由钢板经过冲压、焊接等方式生产而成。在上述轻量化途径中,轻质材料的替代最最为直观且有效的,而铝合金是现阶段的最佳选择。但由于铝合金和钢相比,在物理特性上有非常大的差距,铝合金的连接方式和钢材也有很大的差异,同时不同牌号的铝合金性质差异显著,因此不同牌号之间铝合金的连接工艺的研究就十分有意义。
本文结合电阻点焊以及自冲铆(SPR)两种点连接工艺,以探究这两种最热门技术在7 系和6 系铝合金连接上的应用前景。
试验方法
试样:6061 铝合金板,板厚2.5mm,尺110mm×40mm;7071 铝合金板,板厚2.0mm,尺寸110mm×40mm。其主要化学成分见表1。
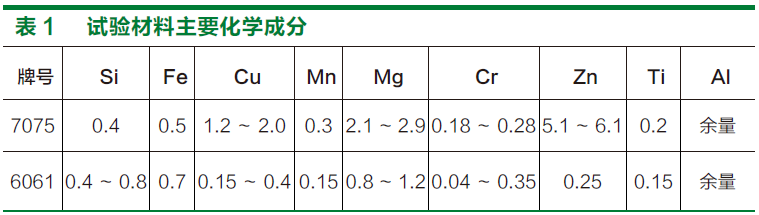
电阻点焊试验分三组:
① 6061-2.5mm+6061-2.5mm;
② 7075-2.0mm+7075-2.0mm;
③ 7075-2.0mm+6061-2.5mm。
焊接后使用万能试验机测试TSS 强度,测量焊核直径。
SPR 试验分三组:
① 6061-2.5mm+6061-2.5mm;
② 7075-2.0mm+7075-2.0mm;
③ 7075-2.0mm+6061-2.5mm。
连接后测量锁铆尺寸(Interlock),剩余材料厚度(Tmin),铆钉高度(Headheight)。
结果与讨论
电阻点焊是将重合的金属夹入相对于的金属电极(焊嘴)上,再加上适当的压力的同时,流过非常大的电流,使之发热熔化,从而接合在一起的焊接。铝点焊与钢点焊一样,应用的都是焦耳原理。同样,点焊的形成可以分为:预压阶段——通电加热——锻压。电阻点焊基本原理图见图1。
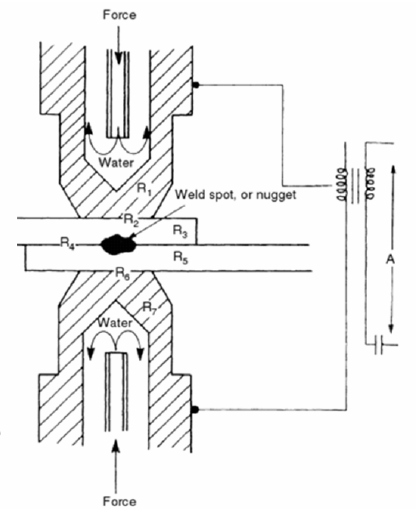
图 1 电阻点焊基本原理
在预压阶段,没有通电流,此阶段电极压力将逐步上升到设定值,通过电极之间的压力作用尽可能使上下板材之间的整度,减少间隙,增大板材之间的接触面积。在通电焊接阶段,采用强焊接规范,即大电流和短时间。因为铝合金熔点低、导电和导热性强,比热容比钢大2 倍,导热性约比钢大三倍,需要在短时间内输入更多的热量的,必须采用能量集中、功率大的热源,才能保证良好的焊接。在通电时,电极与板材以及板材之间均会产生极大的热量,板材之间会逐步熔化形成熔核,而板材与电极之间的热量会被循环冷却水带走。在锻压冷却阶段,电极会在维持一段时间的压力后逐渐减少至零。这个阶段是为了让在通电焊接阶段已经形成了液态焊核在外部的作用力,在理想的冷却条件下形成致密的组织,减少喷溅、缩孔等焊接缺陷的产生。
自冲铆是铆钉在外力的作用下穿透第一层材料和中间层材料,并在底层材料中进行流动延展,形成相互镶嵌的永久塑性形变,这样的铆钉连接技术成为自冲铆,英文简称SPR(Self-piercing Rivet)。自冲铆基本原理图见图2。
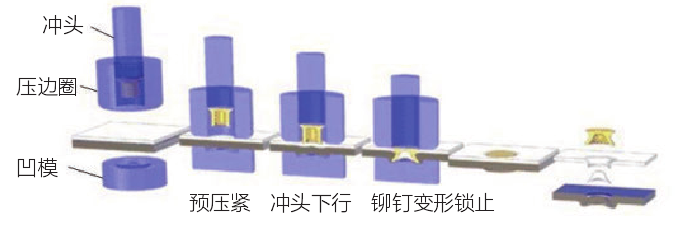
图2 自冲铆基本原理
自冲铆连接的工艺过程包括四个阶段:夹紧——冲刺——扩张——冲铆完成。夹紧阶段,压边圈向下压紧待铆接板料,与此同时,铆钉也在冲头的驱动下垂直向下对板料进行预压紧;冲刺阶段,冲头向下运动,推动铆钉迫使其穿透上层板料,同时铆钉也驱使下层板料向凹模内发生塑性变形。扩张阶段,铆钉腿部逐渐张开,下层板料发生塑性变形逐渐填充入凹模,在冲头和凹模的共同作用下,铆钉腿部向周围扩张,嵌入下层板料从而形成铆钉与板料间的机械互锁结构;冲铆完成阶段:当冲头将铆钉下压至铆钉头与上层板料的上表面紧密接触且平齐时可以认为铆接完成,此时压边圈释放压边力,冲头将返回初始工位,自冲铆结束。
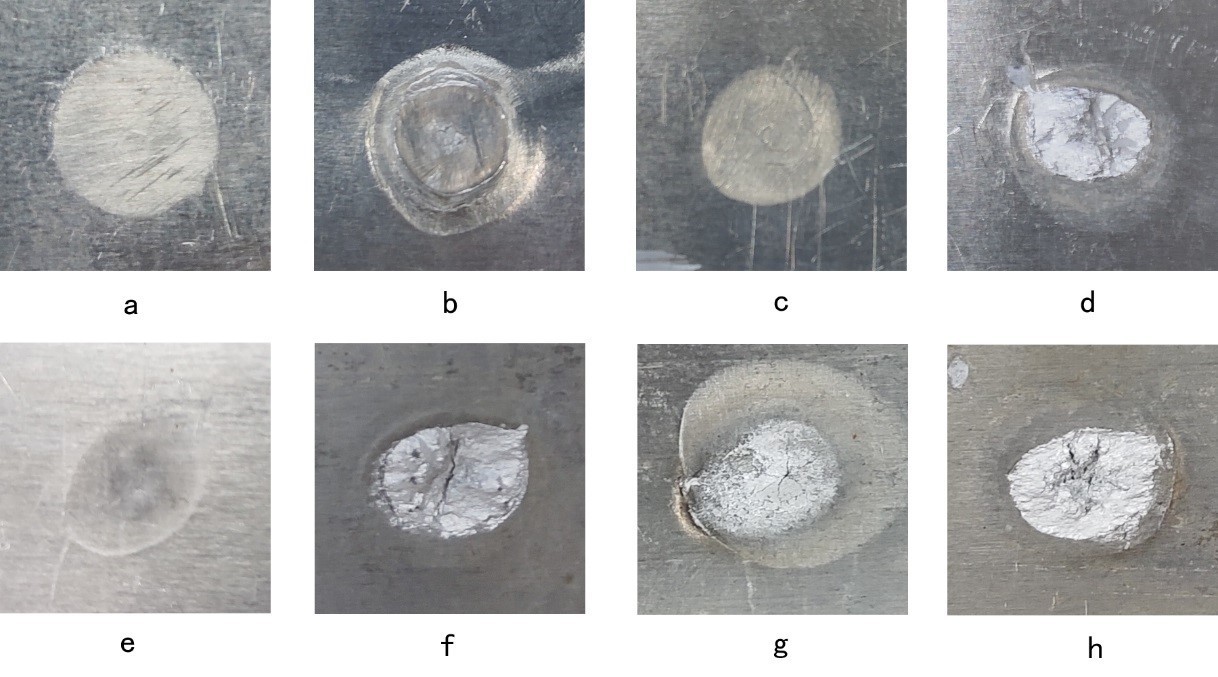
图3 焊点外观形貌以及焊核形貌图
电阻点焊,焊点外观形貌以及焊核形貌图见图3。图a 是① 6061-2.5mm+6061-2.5mm试验组焊点外观形貌,表面平整有光泽,无明显凹陷压痕,是典型合格的电阻焊点外观形貌,图b 是① 6061-2.5mm+6061-2.5mm 试验组,试片撕裂后焊核外观形貌,焊核完全从母材上撕裂,说明形核良好;图 c是③ 7075-2.0mm+6061-2.5mm 试验组6061 一侧试片焊点外观形貌,与图a 基本一致,表面平整,无明显缺陷,图d 是③ 7075-2.0mm+6061-2.5mm 试验组6061 一侧焊点撕裂后,焊核形貌,焊核处凸起,仅有小部分焊核从母材上撕掉,且撕裂结构不均匀,呈现脆性断裂形貌,图e 是③ 7075-2.0mm+6061-2.5mm 试验组7075 一侧试片焊点外观形貌,焊点中心呈黑色,有过烧痕迹,表面微微凹陷,图f 是③ 7075-2.0mm+6061-2.5mm 试验组7075 一侧撕裂后,焊核形貌,焊核部分从母材上撕裂,有明凹陷,且有巨大裂纹;图g 是② 7075-2.0mm+7075-2.0mm试验组,焊点外观形貌,焊点表面呈灰白色,明显过烧,且焊点表面开裂,焊点外观不合格,图h 是② 7075-2.0mm+7075-2.0mm 试验组,试片撕裂后,焊核形貌,与图f 类似,焊核灰白,且充满裂纹。
电阻点焊试验结果见表二。
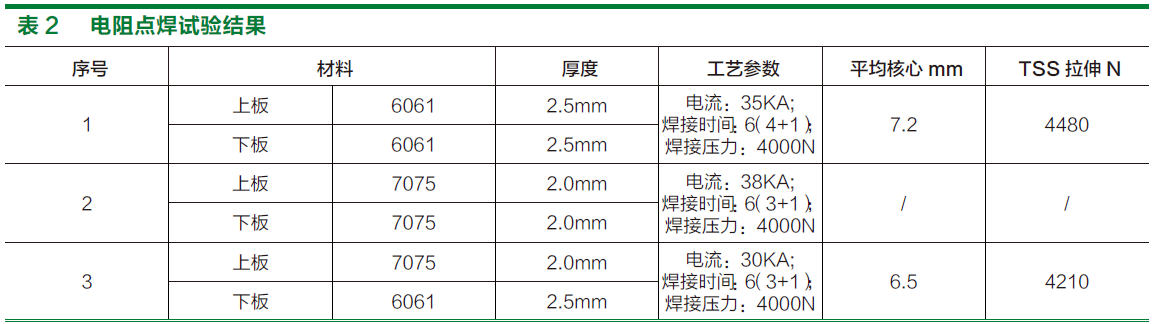
① 6061-2.5mm+6061-2.5mm,电阻点焊性能良好,可以形成良好焊核,平均焊核直径达到7.2mm,平均TSS 拉伸强度达到4480N;② 7075-2.0mm+7075-2.0mm,电阻点焊性能差,无法有效焊接;③ 7075-2.0mm+6061-2.5mm,焊接性能较差,平均焊核直径6.5mm,平均TSS 拉伸强度4210N。
结果表面,6061 铝合金具有较好的焊接性能,可通过电阻点焊形成良好的焊点,而7075 铝合金焊接性能差,无法焊得有效焊点,6061+7075 的搭接形式,有效焊接偏向6061 一侧。产生这样的结果的原因在于,7 系合金含有较多的低沸点 Zn、Mg 合金元素,在焊接过程中烧损严重,熔核区域中强化相( 如 MgZn2) 减少,导致焊接强度降低;7 系铝合金是经固溶、时效等热处理达到较高的强度后使用,在焊接时,焊接区域经历较高温度的焊接热循环,热影响区发生过时效和晶粒粗化而严重软化;同时,7 系合金焊接热裂纹倾向非常敏感,非常容易出现热裂纹,在这些因素的综合影响下,电阻点焊7 系铝合金很难获得理想的结果。
SPR 试验后,横截面形貌以见图四。图a 是① 6061-2.5mm+6061-2.5mm 试验组试片横截面形貌,两层板之间形成了良好的锁铆结构,铆接效果良好;图b 是② 7075-2.0mm+7075-2.0mm 试验组形貌,铆钉仅刺穿第一层,完全没有刺入第二层,铆钉屈服,没有形成锁铆结构;图c 是③ 7075-2.0mm+6061-2.5mm 试验组,7075 为上板,6061 为下板铆接后截面形貌,同样形成了良好的锁铆结构,但锁铆尺寸相比图a 小,图d 是③ 7075-2.0mm+6061-2.5mm 试验组,6061 为上板,7075 为下板铆接后截面形貌,没有形成有效的锁铆结构,铆钉刺穿第一层,并刺入第二层,但未形成锁扣结构,铆钉屈服。SPR 试验结果见表三。
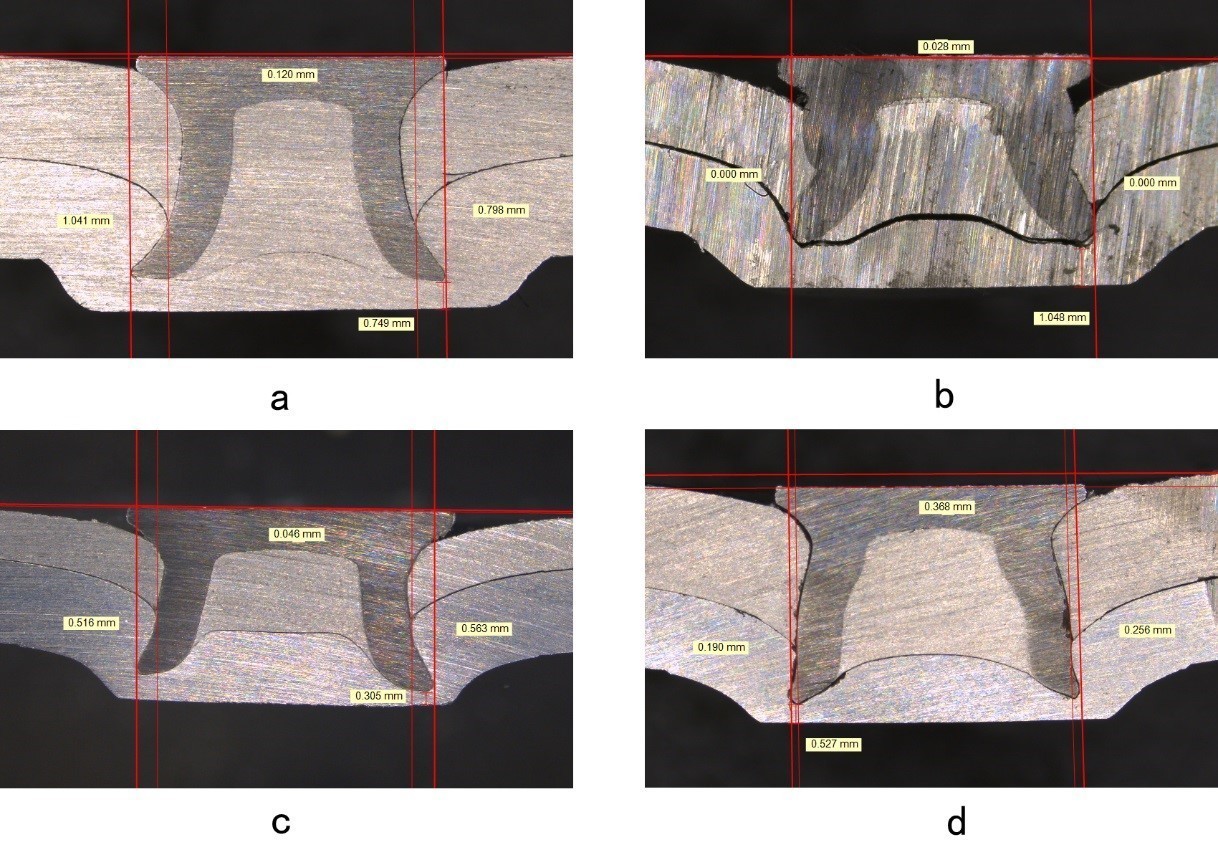
图4 SPR 横截面形貌图

通常,自冲铆需要满足以下条件:底层至少是总厚度的三分之一;强度高的材料在冲模一侧,强度低的在下侧;薄的材料在冲模一侧,厚的材料在下侧。即在铆接时,将厚度较大的板料放在下层,将较软、塑性好的板料放在下层。当实际需求薄而硬的板放置于下板时,或两层板都是薄且硬时,铆接质量就很差。② 7075-2.0mm+7075-2.0mm试验组和③ 7075-2.0mm+6061-2.5mm 试验组,6061 为上板,7075为下板就是这种情况。从结果看,7075 做底板铆接效果均不理想,由于7075 材料强度高,且延展率差,铆钉难以刺穿,导致铆钉本身屈服变形。即使勉强刺穿,7075 板材本身也十分容易开裂,产生铆接缺陷。当7075 作为上层板,6061 做下板时,铆钉刺穿上板后,可以在下板中获得较良好变形条件,从而获得合格的锁铆结构,① 6061-2.5mm+6061-2.5mm 试验组和③ 7075-2.0mm+6061-2.5mm试验组,7075 为上板,6061 为下板即这种情况。

结论
6061铝合金具有较好的焊接性能,可通过电阻点焊形成良好的焊点,而7075 铝合金焊接性能差,无法焊得有效焊点,6061+7075 的搭接形式,有效焊接偏向6061 一侧。
6061铝合金铆接性能好,7075铝合金铆接性能差,当7075 铝合金作为底板时,无法形成有效锁铆结构,当7075作为上板,6061 为底板时,可得到合件铆接结构。
针对7系铝合金连接工艺的选择,尽量避开类似电阻点焊这样过度加热的工艺方案。
SPR连接工艺要求下层板要采用较高延展性的材料,延展性差的材料只能放在上层。